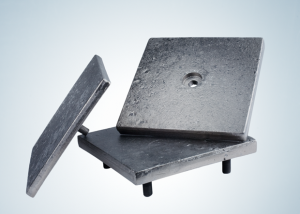
Em uma mineradora sueca de cobre, o HX900 se comprovou eficaz para o aumento da produtividade, redução de custos e melhoria das condições de Saúde, Segurança e Meio Ambiente (SSMA). No Brasil, já está em uso em mineradoras de ouro e ferro e, em breve, será testado em uma mina de cobre. Na mina de ouro, por exemplo, sua durabilidade foi mais de 20 vezes superior ao material anteriormente utilizado, diz Raphael Carmona, gerente de Linha de Negócios da Sandvik.
“O HX-900 é um material antidesgaste composto que combina a resistência a resistência ao desgaste do carbeto de tungstênio com a resistência ao impacto, a ductilidade e a tenacidade do ferro fundido nodular”, explica o gerente. Produzido como compósito ou revestimento – ou numa combinação de ambos -, o método de fundição empregado nos dois formatos cria uma liga metalúrgica entre os grânulos ou telhas de metal duro (tungstênio) na zona de desgaste e o metal de base (ferro nodular). Essas características lhe asseguram a condição de substituir aços convencionais resistentes ao desgaste, ferros fundidos e revestimentos rígidos em peças de desgaste sujeitas a tensões severas e ambientes hostis.
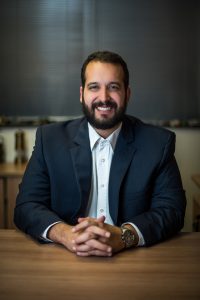
“A capacidade de resistência ao desgaste por abrasão e impacto resulta em uma maior vida útil do HX900 e, em consequência, na maior disponibilidade física do equipamento, com menor número de intervenções para manutenção”, justifica Carmona. O produto tem indicação para a indústria de mineração, siderúrgicas e concreteiras, entre outras, em operações de britagem, fragmentação e moagem, podendo ser aplicado em chutes primários e secundários, alimentadores, chutes alimentadores, chutes de transferência, forros, calhas, moegas e silos.
Comparativos
Em testes de campo realizados nesses diversos equipamentos, o HX-900 demonstrou uma durabilidade até sete vezes maior em relação a materiais antidesgaste fabricados em níquel duro, exemplifica Carmona. Os melhores resultados, no entanto, são dos comparativos com produtos em aço manganês e aço endurecido, onde a durabilidade da liga tungstênio-ferro foi até dez vezes superior (veja tabela)
Em termos de custo-benefício, embora o gerente ressalve que os estudos devam ser realizados caso a caso, dependendo diretamente da aplicação e característica do minério, já foram registrados os ganhos em relação a alguns outros materiais antidesgaste.Os percentuais variam de até 700% para o níquel duro; 800% para o ferro fundido de alto cromo; 1.000% para o aço manganês e chegam a até 1.500% para o aço endurecido.
A facilidade de manutenção e redução dos riscos de segurança operacional são dois outros diferenciais. A primeira, diz Carmona, porque o HX900 dispõe de dois sistemas de fixação – por parafusos ou com parafusos incluso na própria placa. No caso da segurança, a maior durabilidade do material diminui a exposição do profissional da área a espaços perigosos e confinados durante as intervenções corretivas.
Case sueco
Um bom exemplo dessa performance do HX900 é o registrado em uma mina de cobre na Suécia, envolvendo o chute usado para o transporte do material lavrado à etapa de britagem. O impacto do minério danificava o revestimento do chute, exigindo inspeções regulares para sua troca. Nessas ocasiões – por 8 horas a cada quinze dias, totalizando 330 h/ano -, era preciso parar a produção dos três britadores para a entrada da equipe de manutenção no chute único de alimentação. O local era escuro, empoeirado e havia alto risco de lesão pela queda de rochas ou objetos.
Os testes realizados comprovaram que as placas HX900 suportaram 250 mil t de minério antes de serem substituídas, em comparação a cerca de 60/50 mil t de outros revestimentos, com custo total entre três e seis vezes menor. Para a segurança operacional, a equipe da Sandvik, junto à consultoria de engenharia Prime Solutions, desenvolveu um projeto modular para o chute, de forma que ele pudesse ser removido e substituído por um sobressalente, sem interromper a produção e eliminando os riscos de manutenção. Com as mudanças,as paradas de manutenção passaram a ser agendadas com base no desempenho operacional do equipamento, a cada 20 semanas de operação, em média.